
CASE STUDIES
ChemSim has been working with clients in the bioenergy, biomaterial, chemical, and biotechnology sectors
since 2002 to provide a wide range of process simulation services. Below are just a few examples of our projects.
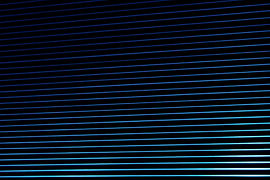
Commercial Biopharma
Production Facility Configuration
OVERVIEW
A commercial biopharmaceutical manufacturing facility needed to address configuration issues to support high titer processes. The client's goal was to identify potential facility and process bottlenecks.
APPROACH AND RESULTS
ChemSim performed throughput analysis at production titers of 2g/L, 5g/L, and 10g/L mAbs. ChemSim identified significant throughput constraints in purification support operations with higher titers, as well as primary constraints with buffer prep and buffer hold vessels. We also identified additional constraints with media prep operations and nutrient hold tanks.
CLIENT OUTCOMES AND BENEFITS
ChemSim's results allowed the client to identify necessary facility upgrades, which justified capital project support. The client was able to make the required changes to the production process to accommodate the manufacture of high titer products.
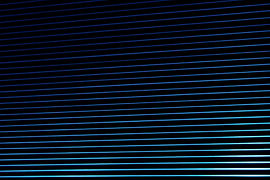
Techno-economic
Analysis for Commercial Bioplastics Production
OVERVIEW
A start-up bioplastics company operating a pilot plant wished to consider options to scale up to commercial production. They reached out to ChemSim to create comprehensive production models of commercial manufacturing processes to determine readiness and feasibility of various options.
APPROACH AND RESULTS
ChemSim developed a flowsheet simulation model for the complete facility.
We then performed conceptual engineering studies to test different plant configurations at different scales. ChemSim created case studies focused on all aspects of CAPEX and OPEX to determine the overall production cost.
CLIENT OUTCOMES AND BENEFITS
The results of ChemSim's simulation models showed the client the capitalization needed for various levels of commercial production. The results allowed the client to determine investment needs and explore options on whether to build a new or utilize an existing production facility.
​
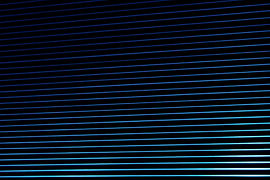
Conceptual Engineering for an Industrial Biofuels Plant
OVERVIEW
An industrial biotechnology company was developing a new process to produce a bioderived heating oil substitute and associated bioproducts. The company hired ChemSim to generate comprehensive material and energy balances that could be used for detailed plant design, scaling of key equipment, and assessing the sizing of utilities.
APPROACH AND RESULTS
ChemSim began by developing a flowsheet simulation model for the complete facility. This approach included detailed physical property models that predicted the performance of key unit operations. ChemSim then performed conceptual engineering studies to test different plant configurations to determine the optimal design. In addition, ChemSim created case studies to test the effect of feedstock composition from various sources to determine the total production of the final product and by-products.
CLIENT OUTCOMES AND BENEFITS
The client obtained the necessary data to support contracting with an engineering and design firm and capitalizing building of a production facility.
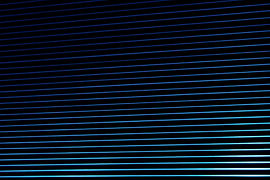
Facility Utilization for a Multi-product Biopharma Facility
OVERVIEW
The client, an international biopharmaceutical company operating a multiproduct facility with multiple trains and a mixture of products of varying campaign lengths, approached ChemSim to model its facility utilization. They wished to compare their current annual production to the potential maximum output given equipment constraints.
APPROACH AND RESULTS
ChemSim created SuperPro models for each of the programs for the multiple trains which were then combined to show the current annual throughput in SchedulePro. ChemSim next created schedules to show the maximum possible throughput and identified the critical path through the facility for each program.
CLIENT OUTCOMES AND BENEFITS
ChemSim's results allowed the client to determine the maximum cost-effective throughput for the facility. In addition, the results allowed the client to identify bottlenecks and potential conflicts with equipment usage and constraints.
​